Die Casting - Advantages of using dieCAS® Software
Unlike other general purpose casting analysis products,
dieCAS®
software is specialized to die casting. As a result, it can take advantage
of die casting's characteristics and achieve enormous savings in analysis
time, without sacrificing solution accuracy. Below table shows die casting
problems versus traditional casting analysis approach.
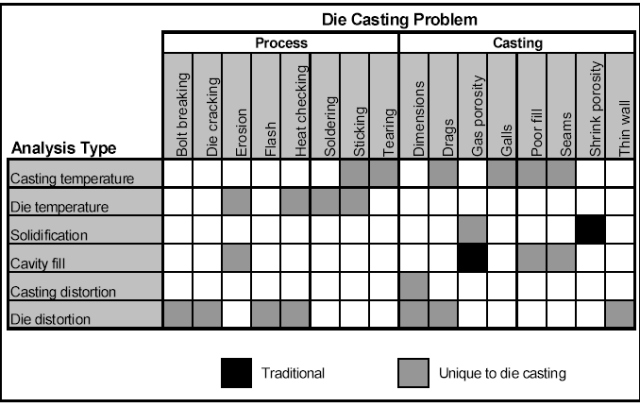
The analysis is based on a shell-like finite element model of the casting
together with a three-dimensional finite element model of the die. This
combination creates the following unique advantages:
- Direct Calculation of the Steady Periodic Die Temperatures. Unlike
all other commercial systems, dieCAS
software does not have to analyze the leading process transient to
calculate die temperatures at steady state. This reduces computer time
from several days (and even weeks for a large die) to a few hours.
- Simplified Model Creation & Editing. Because dieCAS
uses three-dimensional unstructured finite element meshes automatically,
the user has to generate only the surface mesh to create the volume mesh
automatically. This simplifies the process of both creating and editing
the die model. Since cooling lines are represented by one-dimensional
elements in the die interior, they can be altered independently of the
die model.
- Rapid Analysis of Cavity Fill. The unique two-dimensional
representation of the die cavity enables an extremely fast analysis of
liquid metal flow during cavity fill. Cavity fill run times for even
large castings are just a few hours, compared with several days for
conventional methods.
- Complete Thermo-Mechanical Model of Casting and Die Distortion.
Thermal distortions and residual stresses are calculated with minimal
user input after the completion of filling and thermal analyses. All
Results are available in about an hour, even on very large dies
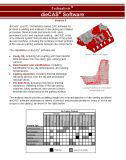
dieCAS
Software
(.pdf file)