Simulation of CVD process - Chemical Vapor Deposition Process
Technalysis specializes in modeling processes involving liquids and vapor
droplets. Technalysis has developed special capabilities solving such
problems. Chemical Vapor Deposition (CVD) Process can be analyzed and
optimized using these capabilities.
Schematic of on-line CVD float glass coater (Example)
Objectives:
- Improve quality
- Increase yield
- Understand critical parameters controlling the process
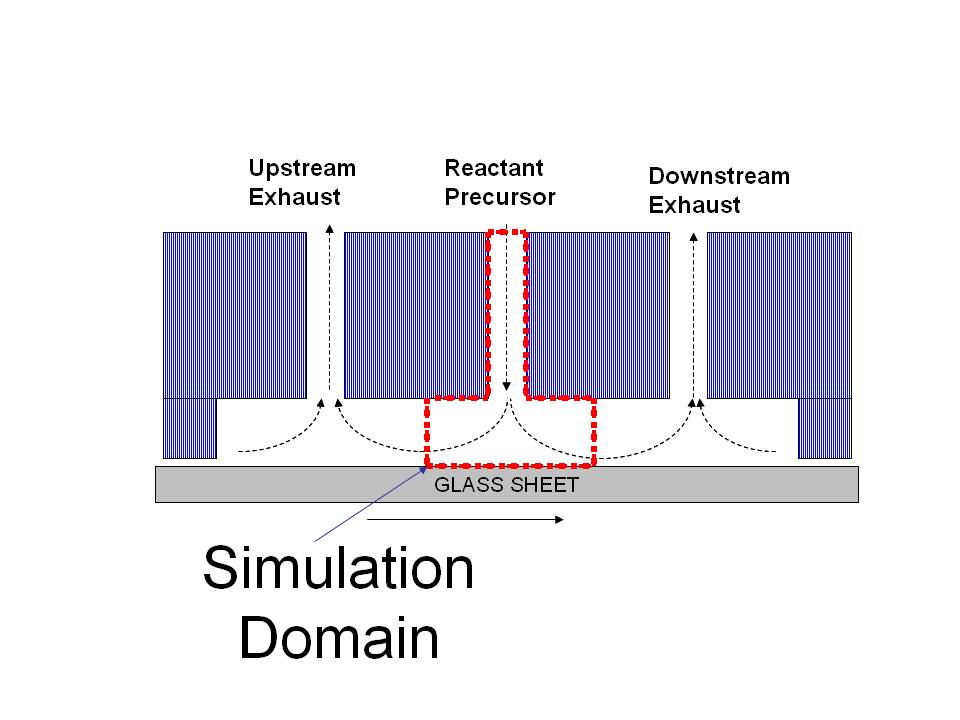
DEM and FLOW Models
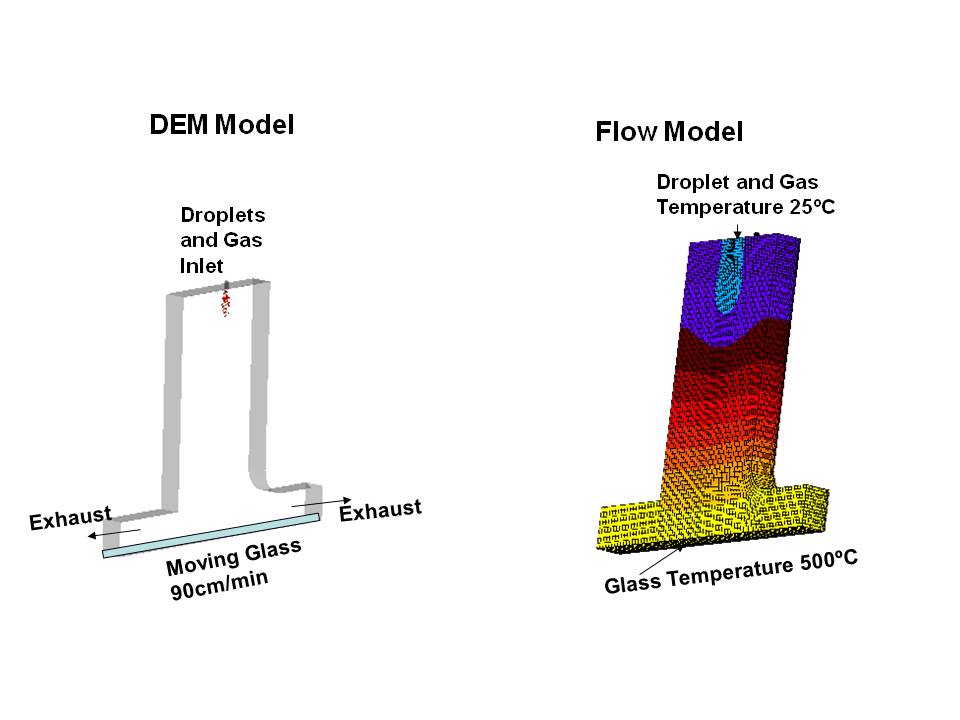
Temperature Distribution and Initial part of Vaporization (Example)
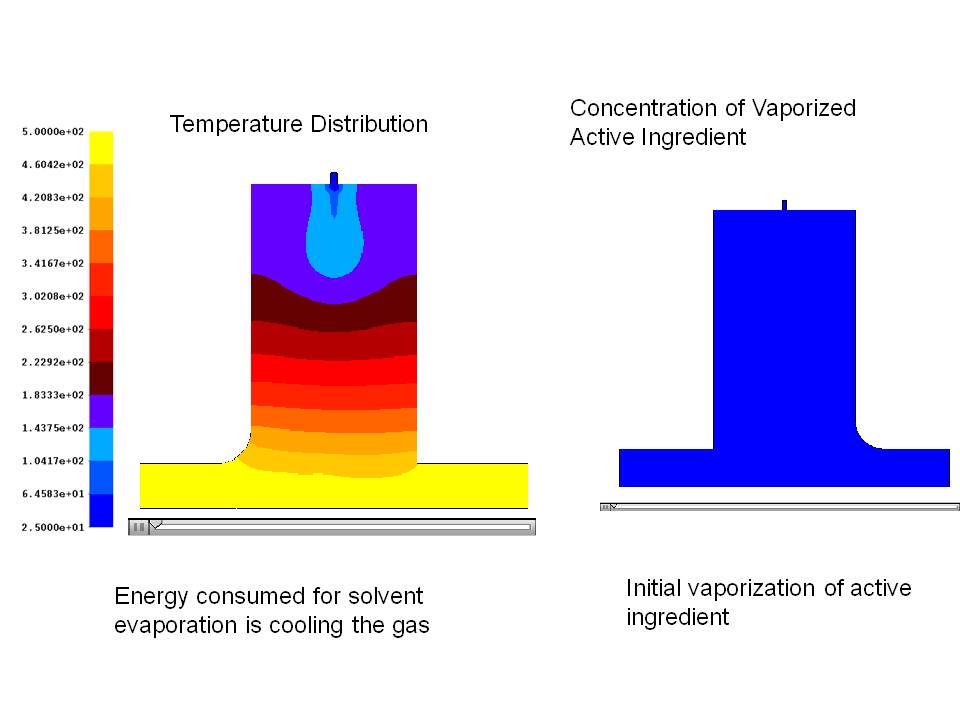
Droplet Size Change during Evaporation inside the Nozzle
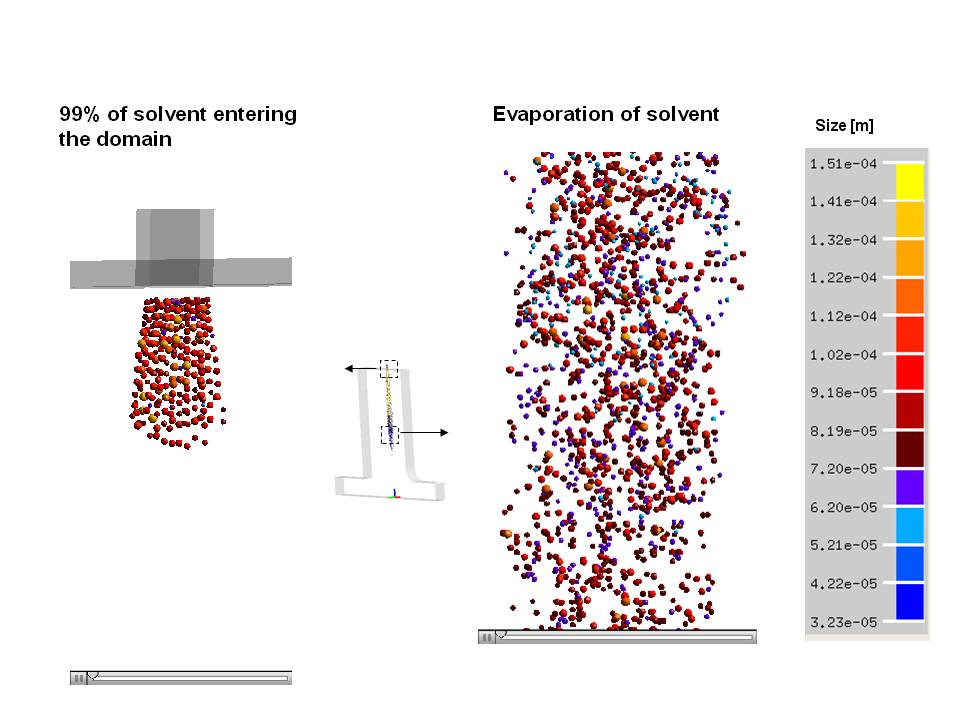
Outcome:
- Reduce scrap by significant amount
- Improve yield by significant amount
- Provided detailed changes to the glass coater
Contact Technalysis to discuss our Chemical
Vapor Deposition (CVD) simulation capabilities in detail.
Advantages of Passage DEM+FLOW
By coupling PASSAGE: Discrete Element Modeling (DEM) and 3D FLOW
software a variety of problems can be solved which can not be
treated by using either one model individually. This capability
allows modeling of liquids, gases, solid particles and their
mixtures for many industrial problems in both micro and macro
scales. It can be applied to process modeling of mixing, wetting,
coating, filtration, fermentation and filling operations for
applications in food, pharmaceutical, chemical, metals, plastics,
glass, ceramics, powders processing and emission control.
DEM and FLOW modules can be coupled
in a variety of ways depending
on the application.
DEM+FLOW
brochure (.pdf)